电解精炼,最新Nature Materials!
催化计
2021-10-01
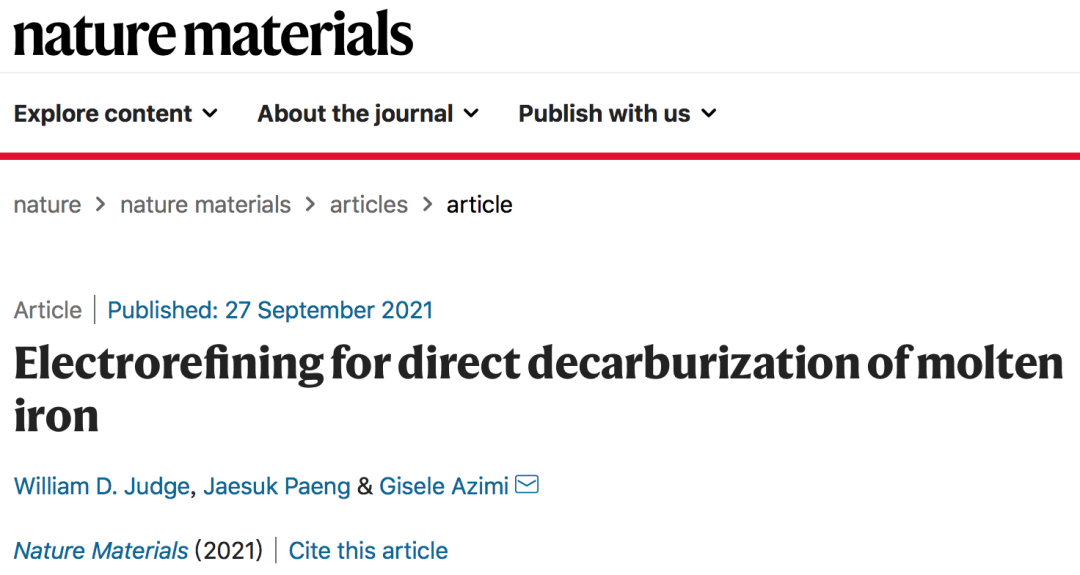
全球资源消耗量现在每年达到惊人的 900 亿吨,这使得对环境的长期可持续发展面临严峻挑战。大多数原始材料的提取和制造过程都是能源密集型,会排放出大量温室气体。因此,材料再利用和回收利用是可持续发展的关键战略。事实上,再利用和回收有助于人们实现循环经济,但这一领域仍缺乏技术创新。在商品金属中,钢铁的回收尤为重要。目前,全世界每年生产大约19亿吨粗钢,炼钢占到了所有人为二氧化碳(CO2)排放量的约 7% 。大多数 CO2来自钢厂初级钢铁生产的直接排放,其中每吨钢约排放2.1-2.6 吨 CO2。同时,在小型钢厂中使用电弧炉 (EAF) 回收废钢每吨钢仅排放 0.4-1.0 吨CO2,大部分 CO2是来自发电的间接排放。 因此,在达到由循环维持的闭环时,CO2排放量将大幅减少。然而,这一结果取决于再生钢的质量是否满足需求。更高质量的钢一直是钢铁消费行业所追求的目标。为了实现循环经济,二次炼钢必须严格控制碳等元素,将低价值的废钢转化为高价值钢。为了满足材料要求,EAF生产的铁水通常需要在几个反应堆中进行处理,需要通过氩氧脱碳、真空罐脱气或再循环脱气进行精炼,才能将碳脱除到较低的水平。虽然这些技术可以脱碳,但它们是间歇过程,消耗试剂,金属会流失到炉渣中。另一个问题是原料的可变性。废铁的成分差别很大,EAF中通常含有一些直接还原的铁,其碳含量高达4%。因此,需要新技术来处理各种原料,以较少的试剂生产高价值的产品。在许多方面,电化学精炼技术能够很好地克服传统技术的局限性。当反应在热力学上不利时,施加电势就会迫使反应继续进行。此外,电力成本相对便宜,EAF小型钢厂已经建成了电力基础设施。然而,迄今为止,电化学精炼的重点还是在碳饱和铁(铁水,由综合工厂中高炉生产)和反应机制上,未实现工业应用。尚不存在用于EAF小型钢厂、脱碳或下游低碳钢生产的电精炼工艺。基于此,加拿大多伦多大学Prof. Gisele Azimi报道了开发了一种电解精炼工艺,通过在铁水和渣电解液之间施加电动势,实现直接铁水脱碳。在阳极极化时,炉渣中的氧化物阴离子直接排放到溶解在铁水中的碳上,形成气态一氧化碳。值得一提的是,这种电解精炼直接通过界面反应实现脱碳,与高度依赖于与溶解氧反应的传统做法截然不同。此外,该技术仅需要低能量输入且无需试剂,便可生产超低碳钢并在阴极回收硅作为副产品。因此,这项技术有望满足二次钢厂未来的需求。在实际生产中,由于碳与氧的高亲和性,且易于脱除的气态产物一氧化碳,所以通常采用氧化来脱碳。工业转炉一般使用气态氧及其通过喷枪和风口吹出的稀释混合物对铁熔体进行脱碳。以这种方式,脱碳不仅在碰撞热点处进行,而且还通过溶解在铁中的氧间接进行。而与传统完全不同的是,研究人员将炼钢炉渣中的氧化物离子电化学放电作为铁水脱碳的途径。其不依赖于中性氧原子或分子与碳的化学反应,而是表明脱碳可以通过释放氧化物离子来形成一氧化碳而无需氧气中间体。为了研究熔渣中铁液的电精炼,研究人员设计了一个电化学池(图1a),并对其进行了概念性操作。采用二硼化锆作为惰性电极连接铁液,从而使得铁液自由极化。对电极在电解槽内垂直定向,并从中心偏移,使得电解槽进行不间断的气体演化和可视化观察(图1b)。脱碳是通过各种铁碳中间合金在充当电解液的氧化物基渣中的阳极极化进行的。该电解槽电位为脱碳反应向极低碳水平进行提供了热力学驱动力。图1b显示,确实观察到在阳极极化时从铁水-碳电极中释放出的气体。在恒流调制下运行,研究人员随着时间的推移跟踪废气成分,并在极化开始时检测到一氧化碳的释放。工作电极(图1d)证实发生了脱碳。电解精炼后,碳浓度从母合金中的 3.78 wt% 降低到 0.84 wt%,电流效率高达 76%。精炼后铁中的总氧含量仅为 0.0054 wt%,表明钢具有高清洁度,并突出了氧化物直接排放在碳上而不是进入铁熔池的趋势。在电解精炼过程中,通过在反电极处发生相等且相反的反应,在电池中保持电中性,反电极在这里充当阴极。在设计的炉渣中含有二氧化硅和其他更具电负性的金属氧化物,以利于硅的回收,研究人员利用这个机会在对电极处回收金属硅作为副产品,方便其在炼钢厂中使用。反电极的表征证实了金属硅的沉积,其与钼基板形成合金(图1e)。考虑到已经确认了碳的去除、一氧化碳气体的产生和金属硅的沉积,研究人员提出了以下总体电池反应:[C] + 1/2(SiO2) = CO(g) + 1/2Si(l) (1)这些结果显示,通过在铁水和炉渣之间施加电动势,可以实现铁水脱碳。有理由相信该过程是直接氧化碳,并且可以通过优化电流或电位调制来进一步提高效率。图1 实验证明电解精炼在1600 °C下对含3.78 wt%碳的铁水可进行直接脱碳根据反应物和产物的消耗和生产,研究人员确定了整个电池反应是按照反应(1)进行的;然而,并没有获得关于阳极半反应路径((O2−)+ [C] =CO(g) +2e−)的信息。研究人员进行了详细的电化学研究,以阐明反应机理并测量其动力学参数。对含不同量碳的合金和纯铁进行了电化学阻抗谱分析(图2a)。结果显示,碳大大降低了电荷转移电阻并增加了合金的界面电容。通过绘制相互电荷转移电阻与合金中碳的化学活性来测试交换电流的依赖性(图2c),在宽的组成范围和接近二分之一的特征斜率上的定量关系表明,碳直接参与剩余电位下的电位决定反应。进一步的,研究人员探索了阳极极化过程中脱碳是如何进行的,得到了稳态极化曲线(图2b)和Tafel交换电流和合金中碳活性之间的关系(图2c)。在选定的半对数图上的线性关系遵循Tafel’s方程,表明在这些选定区域内发生了电荷转移控制下的反应。在1650和1700 ℃的极化曲线验证了Tafel’s方程预测的斜率随温度升高而变陡,交换电流的高激活能(273±2 kJmol-1)与活化控制一致。以Tafel行为为特征的反应代表了涉及碳的不同反应或步骤。在某些电流密度下,极化曲线偏离Tafel行为,表明发生了新的速率决定步骤,或者更有可能的是,传质控制优先。研究人员总结了脱碳反应的可能方案(图2e)。推导出了理论Tafel斜率,并为每种可能的反应方案、速率决定步骤和表面覆盖率交换了当前反应顺序(图2f)。将实验观察结果与可能的速率确定步骤进行比较,发现只有图2e 中的反应 (a)明显匹配。因此,阳极极化期间的速率确定步骤对应于氧化物离子的初始放电:(O2−)+[C]=C(O−)ads+e− (3)研究人员分析了不同合金恒流电解精炼过程中的气体瞬变(图2d)。观察到一氧化碳的释放遵循准一级反应动力学,还观察到表观速率常数与电流无关,即使后者几乎是电流的三倍。基于一氧化碳析出速率常数与电流的无关性,研究人员得出结论,脱碳是按照图2e中的方案(I)进行的。因此,一氧化碳的解吸根据:图2 电化学技术阐明了铁水在1600 °C时的脱碳途径研究人员进一步阐明了脱碳机理按照图3中的示意图进行。碳使析氧反应去极化,从而使氧化物离子的放电直接发生在碳上。脱碳通过一系列单电子转移步骤进行,然后是一氧化碳的化学或物理解吸。在第一步中,氧化物阴离子在金属-渣界面处直接排放到碳上,形成吸附中间体C(O-)ads。研究人员测量了该反应的动力学常数。在随后的步骤中,来自氧化物离子的第二个电子被释放以形成中性吸附中间体C(O)ads。最后,一氧化碳分子从界面物理或化学解吸并成核或加入现有气泡。此外,图3中还描绘了有助于补充界面处碳的电涡流混合现象。研究人员进一步探索了电解精炼的能力并对该技术进行了基准测试。如图4a所示,碳浓度的降低伴随着脱碳电流效率的相应降低。然而,电流效率从未达到零,证明熔融电精炼可以在任何碳浓度下进行。因此,本工作将碳含量仅为0.005 wt%的电精炼铁引入到0.001 wt%以下,并将电精炼作为一种制备超低碳钢的方法。虽然这里的电流效率只有1-2%,但由于电池电流低,电荷和能量损失很小。因此,可以通过优化电池电流或电位来提高电流效率。研究人员密切监测了熔渣中的总铁含量。熔渣中的总铁含量保持在较低水平,但略有上升,接近热力学平衡(图4b,c)。由于交换的电子未知,铁在开路时自然溶解。检测到了熔渣中的FeO和Fe2O3,它们形成了依赖于熔渣中局部电位梯度的复杂平衡。相反,通过考虑单位电荷通过的铁损量,发现在低碳水平下铁损量趋于增加。虽然对于较低的碳含量,每法拉第铁的分数损失看起来很高,但实际上由于电池电流较小,其损失幅度较小。为了降低铁损,通过改变晶胞极性,考察了其从精炼后的渣中电化学回收。作者将铁水作为阴极,铁从渣中沉积回来,其在渣中的浓度大大降低(图4b)。因此,本工作能够从渣中回收损失的铁,提高了工艺的收率。在这里,作者通过电化学方法进行回收,证明了其在降低试剂成本方面的潜在的优势。为了评估钢的洁净度,研究人员测量了铁中的总氧,代表了铁中溶解的氧和来自夹杂物的氧的总和。结果显示,电精炼铁虽然含碳量较低,但其总氧含量极低(图4c)。此处的总氧很可能接近溶解氧,说明有较高的洁净度。低于与碳的平衡溶解度极限的氧水平,进一步证明氧化物离子的放电直接发生在界面处的碳上,而不是它们进入铁熔体。这与增加钢氧化的常规脱碳工艺形成鲜明对比。1)提出了一种用于铁水直接脱碳的电解精炼概念。当铁水阳极极化时,熔渣电解液中的氧化物离子通过一系列单电子转移步骤直接释放到溶解在铁中的碳上,然后脱附气体一氧化碳。随着一氧化碳从阳极释放出来,有价值的冶金级硅在阴极处被回收,作为副产品用于钢铁厂。2)电精炼工艺适用于任何含碳量的铁水,研究人员演示了超低碳钢的生产。此外,电解精炼能耗低,不需要试剂,自混合,可以从炉渣中回收金属。同时,除了满足当前对高质量钢材的需求外,研究人员还预计,由于工艺控制容易以及气体、脱氧剂和耐火材料消耗较低,这可能会节省成本。3)除了作为一个独立的过程运行外,电精炼还可以与现有技术结合使用,以加强精炼。研究人员设想,电炉精炼的主要应用是在EAF小型钢厂回收钢材,这些钢厂拥有现有的电力基础设施,可以生产高价值产品。通过提高回收钢的质量,电解精炼有助于材料闭环,减少资源消耗,并减少炼钢过程中的排放。Judge, W.D., Paeng, J. & Azimi, G. Electrorefining for direct decarburization of molten iron. Nat. Mater. (2021).
DOI:10.1038/s41563-021-01106-zhttps://doi.org/10.1038/s41563-021-01106-z